一个钢铁企业的智能制造之路
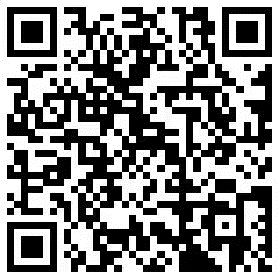
更多精彩请扫描二维码
走进首钢京唐钢铁联合有限责任公司(简称“首钢京唐公司”)运输部5G应用智能仓库,几百米厂房内空无一人,两台无人驾驶的天车在紧张有序地吊装着成品冷轧卷。
首钢京唐公司是首钢搬迁调整的重要载体,是我国第一个实施城市钢铁企业搬迁的企业。在智能制造之路上,首钢京唐公司通过架设工业互联网、云计算、移动APP等网络终端和物联网、智能管控、知识库、大数据等平台,赋能“数字大脑”建设,积极探索企业生产管理新路径,初步体现出智能制造的优势。
物联网成了工厂的“眼睛”
“智能工厂,是一项系统工程。只有持续深化智能制造技术研究与应用,才能保证企业高质量发展方向正确、工作有序、成果有效。” 首钢京唐公司制造部副部长刘文广说。
在京唐公司,物联网技术构建了工厂的“眼睛”。传感器、RFID电子标签代替传统人工监视,海量生产数据通过边缘计算、流式计算与分布式存储技术,实现从“信息孤岛”到“全域集成”的变革。
京唐公司在设备数字化、智慧运维等需求上,建立了数据标准统一、信息安全可控的工业互联网平台——设备数字化智慧运维平台。依托智能运维平台,围绕“设备状态监测”京唐公司设备管理已实现旋转设备振动远程诊断、液压油品状态监测、高压电缆及卷筒局放在线检测等状态监测方式。
“今年8月份刚刚投入的2250热轧粗轧高压液压站介质状态在线监测,对于油品水含量、温度、介电常数等关键指标出现异常,平台会自动出现报警显示,对于滤芯寿命在平台也会有预警提醒,大大提高了管理效率。”京唐公司设备部智能运维中心负责人张本昕介绍说。
5G智能天车的应用,大大提升了生产管控能力和作业效率,经测算提升操作效率10%以上,降低用工需求70%以上,年节约人工成本超过200万元。京唐公司开创了5G+智能化钢铁厂融合发展新模式。
“所有的制造数据在这里一目了然”
走进首钢京唐公司生产管控中心,30多米长、2米多宽的液晶大屏映入眼帘。
“这里集中整合了京唐全流程工艺技术、产品质量、设备运行、能源环境、销售物流、安全消防等数据,充分利用产销平台大数据,实现了数据共享、过程管控、指挥调度、快速响应等功能,形成了数字化、可视化、集约化、扁平化的集中管控平台。”现场工作人员王歆介绍说。
制造部生产管控中心是一个数据中心,但由于专业数据来源分散,专业协同管理缺少及时、准确的数据支撑。“如何解决统计数据多口径问题及数据准确性问题,打通系统间的数据壁垒,是平台建设的重点。” 在集中管控平台开发初期,负责研发的李鹏团队就认识到了理清数据是关键一步。
“在调度职能上,我们对集中管控、区域整合双管齐下,实现扁平化管理。我们还集成了实时天气预报功能,将天气预报与生产计划有机结合。”生产管控中心乙班值班主任郑兴华补充道。
口袋里装着“库房”
打开掌上智能终端,库区内的备件、材料一目了然,领用程序尽在掌控。在首钢京唐公司,数字技术让职工把库房装进了口袋。
为实现实物流、信息流、资金流实时同步,首钢京唐公司依托产销一体化组织开发了设备仓储信息化系统手机终端。此系统将采购系统、设备系统、投料系统与二维码技术相结合,依托移动端实现机旁管理“专业化、信息化、人性化”的智能管理平台。
“以前为了领用一个小小的备件,我们需要记录数据参数、反复核对型号、不断核查现场。现在只要打开手机APP,通过手工录入或者现场扫码,就可以直接查询和操作,及时又高效。智能技术正在改变我们的管理模式。”炼铁部机旁管理负责人蔡金红感慨地说。2022年1~9月,通过系统调拨借用备件,减少采购浪费和库存积压1388万元。
随着自动化控制、5G、人工智能、机器人等先进技术陆续引入,首钢京唐公司智能化管控平台拥有了63个子系统,数据的实际利用率将提升至95%以上;系统平台接入点增加到近6万个;实现端到端数据延时小于2毫秒,全面实现工序多专业、多部门系统作业和信息化管理,打造“统一平台、多级融合、流程闭环、协同管控”的智能化运行平台。天眼查数据显示,我国现有钢铁企业1.4万余家,首钢京唐公司的智能制造之路,可以给这些企业提供参考和借鉴。